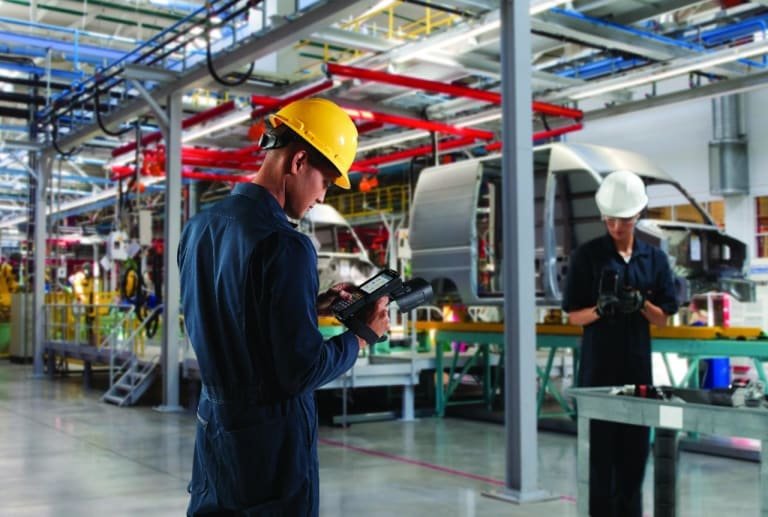
Using RFID for Work-in-Process (WIP) Tracking
Many production floors have become complex and error-prone environments, with complex assembly processes, intricate logistics and countless parts and tools moving about. This creates a serious challenge for tracking and managing it all, especially at a time when there’s more pressure than ever to cut costs and increase efficiency.
In particular, work-in-process (WIP) tracking has become vital in many manufacturing and other production operations. Companies need real-time visibility into their processes to manage all those parts and tools moving around, all the logistics and assembly, and ensure productivity, accuracy, efficiency and quality. One way to do this is by using radio frequency identification or RFID technology.
RFID provides a way to automatically capture information about the items, people and processes critical to your operations. Many manufacturers have become familiar with RFID in their warehouse, where it can be used to tag and wirelessly track inventory. RFID tags allow materials, finished goods, pallets, shipments and virtually any asset to be identified and located automatically and remotely, without having to manually scan barcodes or have line-of-sight to collect data.
However, RFID also has many additional applications on the plant floor, including using it for WIP tracking and simple exception reporting. A great example is using visual aids to alert a worker when an item is brought to the wrong location. You can do this by using a stack light to provide the visual alert.
At Strategic Systems, we’ve installed systems like these using our StrategicRFID software solution. It allows you to set rules and alerts for exceptions like this example. The software automatically detects the item’s RFID tag, matches it against the rule you’ve defined, and detects when the wrong item is brought to the process location.
The software can also be configured to turn on a red stack light when an item skips a step in your process, and it can even send email alerts to management. In turn, management can use the alert data in real-time or after the fact to help improve process accuracy and efficiency. For example, repeated exceptions could indicate a problem with a specific worker or process.
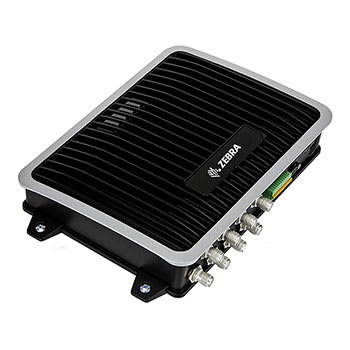
RFID can also provide crucial analytics to help plant managers or process engineers confirm proper flow. For example, RFID tags and software also enable the use of time stamps to track all the assets that move through each stage of a process. This means you can easily measure the average time spent at each step and potentially identify bottlenecks or other timing issues.
When smart RFID tags are introduced into the production environment, you can make more informed decisions about production, inventory levels and delivery dates. As a result, your labor needs and errors decrease, and your costs do too.
Exploring and getting started with RFID for WIP tracking is easy. Our experts can conduct a complete RFID assessment to help you learn more, discuss your specific needs, and determine if RFID is the right fit for your production floor.
The good news is that RFID is now more affordable than ever before, thanks to technology advancements and increased adoption. And our StrategicRFID software costs a third less than traditional RFID software, allowing more companies to integrate RFID in their operations.
It’s a simple web-based application that’s available as a subscription, with nothing to install. Built-in configuration tools make it easy to integrate it with other apps or systems. StrategicRFID is also designed to work seamlessly with industry-leading RFID technologies, including readers, antennas, handheld devices and tags from Zebra, the global leader in RFID.
To learn more, contact our RFID experts now.